Inhaltsverzeichnis
What is TFP - Tailored Fiber Placement?
Tailored Fiber Placement (TFP) is often described by experts as a revolution in industrial manufacturing.
Finally, technical embroidery makes it possible to produce perfectly fitting semi-finished products, the so-called preforms, in a reproducible manner. These are characterized by an extremely strong structure that is structure. Fiber preforms also have other impressive properties, from which different industries can profit massively.
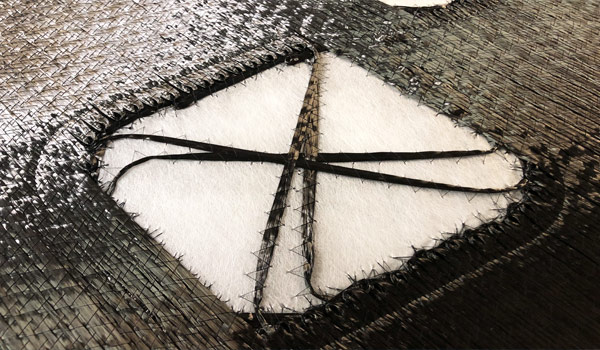
Reinforcing structures / semi-finished products
Textile reinforcement structures can be made from a wide variety of fibers, the best known being carbon, fiberglass, aramid, steels, but also basalt, ceramics, hybrid fibers and natural fibers.
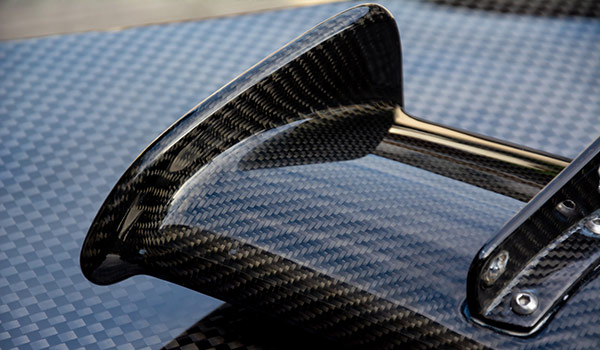
Lightweight components as an application example
With every gram of weight saved in vehicles, aircraft and shipping, fuel consumption and the associated fuel consumption and the associated CO2 emissions are reduced in the long term.
What are preforms and textile semi-finished products?
In the manufacture of fiber composite components, the intermediate stage of the actual component is called the
Preform or preform and can be achieved by various textile processes.
Textile semi-finished products are also a preliminary stage of the subsequently finished component and can be produced with the aid of
technical embroidery, be produced with reinforcing structures.
For example, the embroidery technology is very well known in racing and among fans of fast sports cars.
After all, the advantages of TFP Tailored Fiber Placement are inextricably linked with Formula 1.
Without it, this sport would not be the one they know and love. This begs the question:
What exactly is TFP or Tailored Fiber Placement? This article will tell you.
A short trip to nature: fiber composite parts as inspiration
Fiber composite material is often found in nature. Its geometry and reinforcements are adapted
to the stresses occurring in the environment. Grasses, bones and trees are good examples of this.
examples. Their structures withstand the regional challenges to enable the required
growth required. Without them, life on site would be unthinkable.
This natural principle also comes into play in TFP Tailored Fiber Placement. The reinforced
fiber composite components are usually placed along curved load paths. This requires a
the rovings to the textile or non-textile substrate. This is achieved with the aid
of a sewing thread. However, this design of the fiber scrims is not enough.
Special embroidery equipment is also required if the components are to be processed with a
are to be processed to fit exactly. The machinery is modified and always in industrial use.
use. In addition, the integration of special CAD software is essential to produce fiber placements based on
of Tailored Fiber Placement.
It is also important to understand the nature of the fiber composite components and their structures.
They have an adapted thickness distribution as well as a load-appropriate design and composition.
Conversely, they bring with them an above-average lightweight construction potential. In this context
The automated and additive TFP process offers an attractive reproducibility of fiber preforms.
The amount of waste in Tailored Fiber Placement is also predictably low, similar to 3D printing.
This is not only good for the environment.
Why Tailored Fiber Placement?
TFP Tailored Fiber Placement is a special manufacturing process for preforms.
These are variable-axial. The orientation of the planes can be
planes can be designed as desired. This allows you to make optimum use of the properties of the fiber composite material.
Furthermore, thanks to the forming of the components, it is possible to realize three-dimensional preforms.
This makes Tailored Fiber Placement a valuable all-round technology that offers advantages in a wide range of industries.
advantages in a wide variety of industries.
In view of these properties, another special feature of the Tailored Fiber Placement process becomes clear.
process becomes clear: It represents a further development of the current processing technology. Translate
the term, this quickly becomes clear. The process can also be described as tailored fiber placement.
However, this is not as new as many producers would like to assume. Already at the beginning of the
1990s, TFP Tailored Fiber Placement was brought to public attention by the Leibnitz Institute for Polymer Research.
The basic features remain unchanged 30 years later: They are based
auf der langjÀhrig erprobten Sticktechnologie.
But why was it necessary to further develop the processing technology used to date? This can be
simple to explain: The conventional building blocks could be laid like a film. They were
were woven mats. If three-dimensional structures were to be produced, various problems arose.
problems arose. One of these was the wrinkling that resulted from the inflexible fiber scrims.
fiber scrims. As an irregular body, they had almost no stretching capacity. This resulted in the
constant strength according to the weave structure. This was valid independently of the fabric web, its
direction and the woven mat.
A practical solution for this and other challenges therefore had to be found.
TFP Tailored Fiber Placement as an efficient embroidery technology provided this.
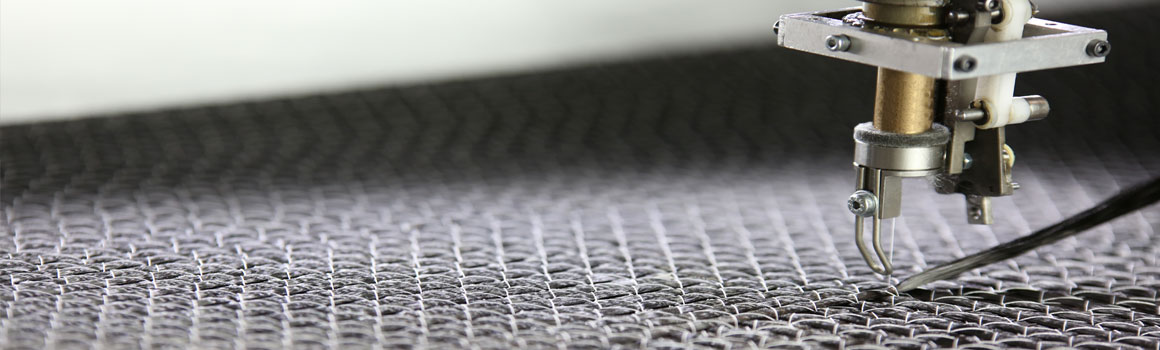
TFP Tailored Fiber Placement offers these advantages
Tailored Fiber Placement was originally conceived to optimally follow the load paths of three-dimensional
three-dimensional components. This is achieved, for example, with the aid of carbon preforms. These strands can be
Tailored Fiber Placement (TFP) allows these strands to be placed in a correspondingly load-path-optimized tray.
In addition, the rovings can be arranged according to requirements. Due to the Tailored Fiber
Placement process, the applied forces of the fiber composite components can be optimally dissipated.
This results in a major advantage in industrial production:
The semi-finished products produced are ideally suited to the particular application. Their strength is
uncompromisingly demand-oriented. This requires the use of special CAD software.
It helps to pre-plan the individual fiber composite components for the individual requirements.
Further processing of the preforms can then begin. The advantages of embroidery technology
clearly speak for themselves during this process and beyond:
High load capacity of the fiber scrims
In TFP Tailored Fiber Placement, fiber composite components are manufactured with an optimum ratio of weight to strength. The individual composite components thus have an above-average above-average load-bearing capacity. This applies to both static and dynamic loads. loads. In view of these properties, it is clear that the fiber-reinforced composite components produced under Tailored Fiber Placement always impress with their demand-optimized advantages. They are therefore fiber composite material made to measure.
Moldable flexible for individual needs
Despite their strength, the fiber composite components manufactured using Tailored Fiber Placement are are uncompromisingly flexible. Even in their three-dimensional form, the fiber composite material can be machined to can be machined to size. This property makes the TFP-based carbon preforms all-rounders in demanding in demanding environments.
Tailored Fiber Placement protects the environment
Another major advantage of the TFP Tailored Fiber Placement embroidery technology is its environmental friendliness. This is achieved thanks to the enormous reduction in weight combined with a low level of waste in the production process. Lightweight materials and lightweight construction in general are an increasingly important topic and, especially in terms of environmental protection and climate change! Every gram of weight saved in vehicles, airplanes and of weight saved in vehicles, aircraft and shipping reduces fuel consumption and the associated CO2 emissions can be reduced sustainably and in the long term. This saves resources and protects the environment!
How Tailored Fiber Placement works - an overview
Textile fiber scrims and carbon preforms can be easily produced using the TFP process. The same applies to semi-finished products and reinforcement structures for fiber composite components. This is possible thanks to different roving material fabrics as a basis for customized processing. Fiber-reinforced plastics, for example, are also the so-called composites. They are made of fibers and resins. To form them in the TFP Tailored Fiber Placement process, they are
embedded in a matrix. This usually consists of epoxy or polyester resins, so-called
thermosets or polypropylene, polyamide so-called thermoplastics. Once the composite components are
Once the composite components are finished, their glass fiber-reinforced form is called GFRP composites. CFRP composites are
when it is the carbon fiber-reinforced variant.
Different manufacturing processes are used in the embroidery technology. These are
On the one hand, this involves RTM or resin transfer molding, which describes a pressure resin
This describes a pressure resin injection process that is characterized by high laminate quality. The molds required for this
molds are closed.
On the other hand, fiber composite material is obtained with the aid of reaction injection molding. Its
abbreviation is RIM. In this process, new fiber composite components are produced from a combination of PUR foam and GRP composites.
fiber composite components. These are stiff, but also very light.
TFP Tailored Fiber Placement also uses the so-called hand lay-up process.
This is the oldest known manufacturing method for fiber scrims. In this process, dry fiber mats are placed in
open molds. These are single-skin. The incorporation of fabric is also possible with this
possible with this manufacturing process.
If prototypes or small batches are to be manufactured using tailored fiber placement embroidery technology
vacuum infusion proves its worth. This involves draping dry fibers into a tool and fixing them in place.
This is a single-shell mold.
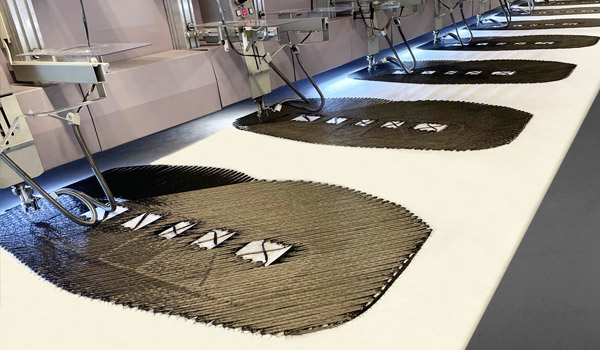
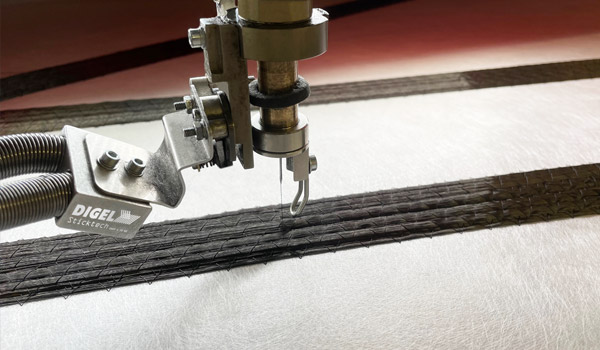
Is Tailored Fiber Placement the textile revolution?
Is Tailored Fiber Placement revolutionizing the industry? To answer this question, it is worth taking a
a look at the past. Fiber composite technology, for example, is not a novelty in itself. In
industrial production in Germany for more than a century, it has been one of the mainstays for a wide
for a wide variety of processes. This gives us an idea that tailored fiber placement will continue to play an important role in the future.
The same applies to science.
Comparing fabrics such as weavable carbon fiber mats and embroidery technology is worthwhile in any case.
After all, both are processes that can be automated to an above-average degree.
automation. Fiber composites can be processed efficiently and carbon preforms are produced quickly.
The cost factor is also convincing thanks to the high degree of automation of TFP.
Moreover, fiber scrims or carbon preforms are not only efficient to process. They are also convincing
strength and low weight, depending on the requirements. As a result, tailored
fiber placement embroidery technology could be used in the future for the production of numerous goods.
machines, sports equipment or even goods are possible examples of this.
examples of this. The construction industry is also likely to benefit from the advantages of the Tailored Fiber Placement
process.
Our Tailored Fiber Placement products and services?
Technical embroidery is an exciting topic and especially the field of TFP is incredibly versatile. Take a look at our Tailored Fiber Placement products and services and convince yourself of our know-how in this field.